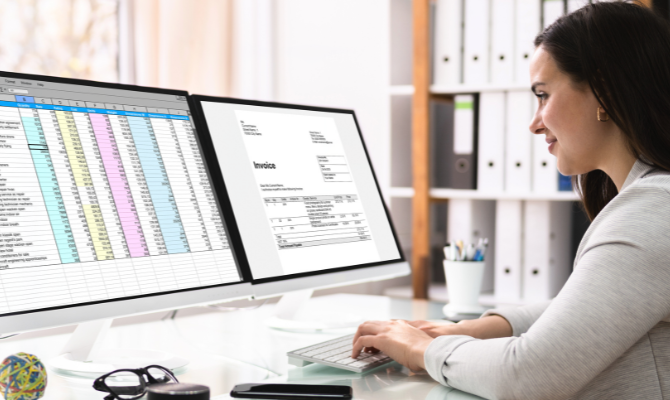
In the ever-evolving landscape of business, efficiency and accuracy are not just desirable, they are essential for success. For far too long, many businesses have relied on spreadsheets and Excel to manage procurement, production, and inventory. However, as complexities grow and demands increase, the limitations of these manual methods become apparent. In this blog post, we will explore the inadequacies of relying solely on spreadsheets and make a compelling case for integrating procurement, production, and inventory management through a comprehensive and user-friendly system.
The Spreadsheet Conundrum-
Spreadsheets have long been the go-to tool for managing various aspects of business operations. While they offer a familiar interface and a degree of flexibility, they come with inherent limitations. As businesses expand and operations become more intricate, the drawbacks of using spreadsheets become pronounced-
1. Prone to Errors- Manual data entry increases the likelihood of errors, leading to inaccuracies in procurement, production, and inventory records.
2. Limited Collaboration- Spreadsheets lack real-time collaboration features, hindering seamless communication and coordination among different departments.
3. Time-Consuming- Updating and cross-referencing data across multiple spreadsheets is time-consuming, diverting resources from more strategic tasks.
4. Scalability Challenges- As businesses grow, managing data in spreadsheets becomes unwieldy and impractical, impacting overall scalability.
The Integrated Solution
The need for a comprehensive and integrated system becomes evident as businesses strive for operational excellence. Here's why an integrated procurement, production, and inventory management system is the key to overcoming the limitations of spreadsheets-
1. Real-Time Data Accuracy
An integrated system ensures that data is entered once and reflects instantaneously across all relevant modules, minimizing the risk of errors.
2. Enhanced Collaboration
Teams can collaborate seamlessly with shared access to real-time data, promoting transparency and efficient communication.
3. Time Efficiency
Automation of routine tasks reduces manual efforts, allowing employees to focus on strategic initiatives rather than spending time on data entry and reconciliation.
4. Scalability
Integrated systems are designed to scale with the business, accommodating increased data volumes and transaction complexities effortlessly.
5. Holistic Visibility
Gain a 360-degree view of procurement, production, and inventory activities in a single interface, enabling informed decision-making based on real-time insights.
Justifying the Need-
The limitations of spreadsheets become increasingly apparent as businesses strive for efficiency and growth. An integrated system not only addresses these shortcomings but also offers additional benefits such as-
1) Reduced Costs- Minimize operational costs associated with manual errors, excessive time spent on data management, and inefficient processes.
2) Compliance Assurance- Ensure adherence to industry regulations and standards by leveraging an integrated system with built-in compliance features.
3) Customer Satisfaction- Efficient inventory management and production processes lead to better customer service and satisfaction, ultimately contributing to customer loyalty.
Conclusion-
The era of relying solely on spreadsheets for managing procurement, production, and inventory is fading. Businesses need a robust, integrated system that combines user-friendliness with comprehensive functionalities. By making the switch, organizations not only overcome the limitations of spreadsheets but also position themselves for sustained growth, operational excellence, and a competitive edge in the marketplace. It's time to embrace the power of integration and leave spreadsheets in the rearview mirror.
The need for a comprehensive and integrated system becomes evident as businesses strive for operational excellence.
![]()
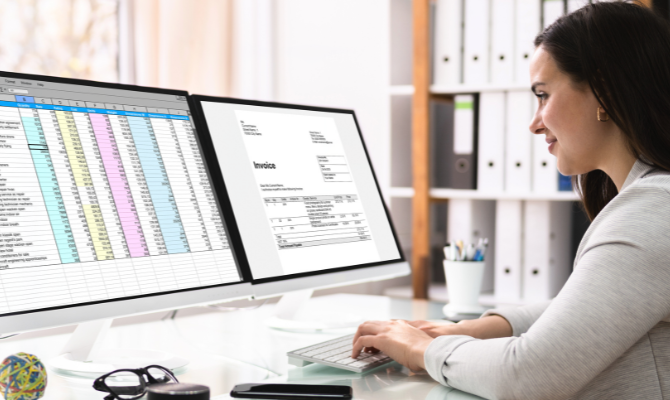